Most Common Vending Machine Repair Issues and Fixes
When I started my vending business, I thought the hardest part would be finding good locations. Turns out, one of the most important skills you need is learning how to fix your machines when things go wrong—and they will go wrong. Whether it’s a coin jam, a product not dropping, or a card reader error, knowing how to diagnose and fix vending machine issues will save you time, money, and customer frustration.
In this post, I’ll break down the most common vending machine repair problems I’ve personally faced, along with simple, actionable solutions you can try yourself—no technician needed (most of the time).
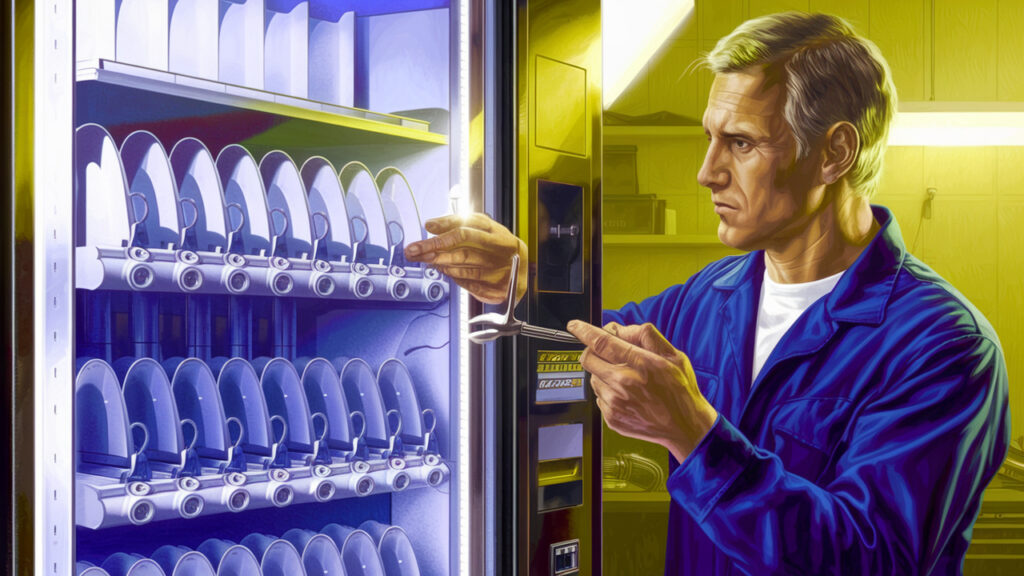
Table of Contents
Problem: Product Gets Stuck and Doesn’t Drop
This is probably the most common issue. A customer makes a selection, the coil spins, but the snack gets caught or doesn’t fall completely.
Fix:
- Use dual coils for lighter or oddly shaped items.
- Avoid stocking bags that are too thin or underfilled.
- Slightly adjust the coil spacing or tension using a screwdriver if your machine allows it.
- Always test new products before fully loading the row.
If it happens often, I remove the product completely and replace it with something that drops clean every time.
Problem: Coin Jam or Coin Not Registering
You’ll notice this when coins get stuck or the machine stops recognizing them entirely.
Fix:
- Open the coin mechanism and clear out any dirt or bent coins.
- Spray electronic-safe contact cleaner into the coin path to remove dust or residue.
- Make sure the coin mech is aligned properly inside its mount.
- Test with newer coins—sometimes older or worn coins won’t register correctly.
✅ CRC Contact Cleaner – Safe for Electronics
Problem: Bill Acceptor Won’t Take Money
This one frustrates customers quickly. The bill keeps getting spit out or the machine won’t respond at all.
Fix:
- Clean the bill reader sensors with a soft cloth and rubbing alcohol.
- Make sure the bills are inserted straight and aren’t crumpled.
- Recalibrate or reset the bill validator.
- Some bill validators need updated firmware for newer $5 or $10 bills—check the manufacturer’s site.
✅ Universal Bill Acceptor Cleaning Cards
Problem: Credit Card Reader Not Working
This is a growing problem as more machines go cashless. If the card reader isn’t connecting or processing, it kills sales fast.
Fix:
- Check your cellular signal—if it’s weak, the reader won’t connect.
- Reboot the card reader and check for firmware updates.
- Make sure your SIM card or data plan is still active (PayRange, Nayax, etc.).
- Clean the reader face with alcohol wipes.
Sometimes just unplugging and reconnecting the power fixes minor software bugs.
Problem: Machine Doesn’t Cool Properly (Drink Machines)
Warm sodas? That’s a red flag. If your drink machine isn’t cooling, don’t ignore it—it will lead to complaints or spoiled stock.
Fix:
- Check the airflow at the back—a blocked or dusty vent can prevent cooling.
- Clean the compressor coils (usually behind the unit).
- Listen for the compressor fan—if it’s silent or struggling, it may need replacement.
- Make sure the machine isn’t in direct sunlight or a tight corner with no airflow.
✅ Foam Coil Cleaner for Refrigeration Units
Problem: Keypad or Buttons Not Responding
If certain selections don’t work, it could be the keypad. This often happens with age or exposure to humidity.
Fix:
- Unplug the machine and check the cable connections to the keypad.
- Clean any debris or stickiness around the buttons.
- In older machines, you may need to replace the keypad membrane entirely.
Most keypad replacements are affordable and take under 20 minutes to install.
Problem: Vends Two Items or Misaligns Products
Sometimes the coil rotates too far and drops two items—or doesn’t align properly.
Fix:
- Reset the motor home position using the service menu.
- Inspect the coil to ensure it’s not bent or over-tightened.
- Make sure the product isn’t too wide or too light—it can trigger incorrect rotation.
Always calibrate the machine after making adjustments to the motor or shelf alignment.
Problem: Machine Won’t Turn On
This one can be alarming, but most of the time, it’s a power issue—not a dead machine.
Fix:
- Check the power outlet and try another device in the same plug.
- Inspect the machine’s internal power switch (usually near the coin mech).
- Look for tripped breakers or blown fuses inside the machine.
If you’ve ruled out all basic issues and it still won’t power up, the control board may need to be replaced.
Problem: Screen Displays Error Codes
If your digital display is showing error codes (like “Vend Error,” “Motor Jam,” “Out of Service”), don’t panic.
Fix:
- Look up the error code in the machine’s manual.
- Most errors are related to motor jams, payment failures, or inventory sensors.
- Clear jams, restock products, or power cycle the machine.
I keep a printed list of error codes taped inside the service door for quick reference.
Final Thoughts
Learning how to handle common vending machine problems has saved me thousands in repair calls. You don’t need to be an expert technician—you just need to be observant, proactive, and patient. Keep a small tool kit, cleaner, and spare parts in your vehicle, and you’ll solve most issues on-site in under 20 minutes.
One lesson I learned early is that preventative maintenance is easier than emergency repairs. I now schedule a quick 10-minute checkup every time I restock a machine. I wipe down sensors, test a couple selections, and check coin and bill acceptors—even if they seem fine. This simple habit has helped me avoid bigger breakdowns down the road.
Keep a vending repair kit in your vehicle. Mine includes a basic screwdriver set, needle-nose pliers, microfiber cloths, alcohol wipes, super glue, contact cleaner, spare fuses, and a voltage tester. I’ve fixed machines on-site that other vendors would’ve shut down for days waiting on parts.
Humidity is another silent killer. In certain locations—like gyms, indoor pools, or laundromats—humidity can cause buttons to short out or displays to fog up. In those spots, I add small moisture absorbers inside the machine to help prevent long-term damage.
If your machine is outdoors or near an open door, make sure you inspect it for pest activity. I’ve found ants inside payment compartments and even small spiders in the coin mech. A quick look inside and some peppermint oil spray can keep those surprises to a minimum.
Label your machine’s internal wiring and parts as you get more familiar. I use a label maker or tape with a Sharpie to tag connections, power switches, or parts I’ve replaced. When something goes wrong later, it’s way easier to troubleshoot if you’ve already mapped things out.
For touchscreen or newer digital models, keep firmware files and a USB drive handy. Some card readers or control boards require updates every few months. I download updates from manufacturer websites and keep them on a flash drive in my glove box so I can update on-site.
Sometimes, vending machines seem fine until temperature changes hit. A machine that worked all summer might suddenly freeze up or trip a fan error once winter hits. I’ve had to realign door gaskets or add weatherstripping to keep the machine operating consistently through seasonal changes.
It’s smart to set up text alerts or email notifications from your card reader provider. PayRange and Nayax both offer alerts for issues like failed transactions or offline machines. These real-time notifications let me respond fast—often before the customer even calls.
If a machine gets repeatedly jammed in the same spot, check the product packaging dimensions again. Even a ¼ inch difference in width or thickness can cause spirals to behave unpredictably. I keep a digital caliper to measure products before adding anything new to the lineup.
I also suggest keeping a small stash of spare motors and keypad parts at home or in a toolkit. A replacement coil motor or keypad costs under $50 and can save you from waiting days for a shipment when your machine is down. It’s a small investment that pays off big.
Another fix that’s often overlooked is the door latch and alignment. If the door isn’t sealing correctly, it can affect internal temperature, power delivery, or even stop vending altogether. I once spent an hour troubleshooting what ended up being a slightly warped hinge from constant slamming.
Lastly, take photos or videos of any unfamiliar issues and save them to a folder. I’ve sent clips to tech support teams or shared them with other vendors online for faster diagnosis. Sometimes just having a record helps you notice patterns or recurring issues across different machines.